Category: Success Story
Form meets function in packaging design program
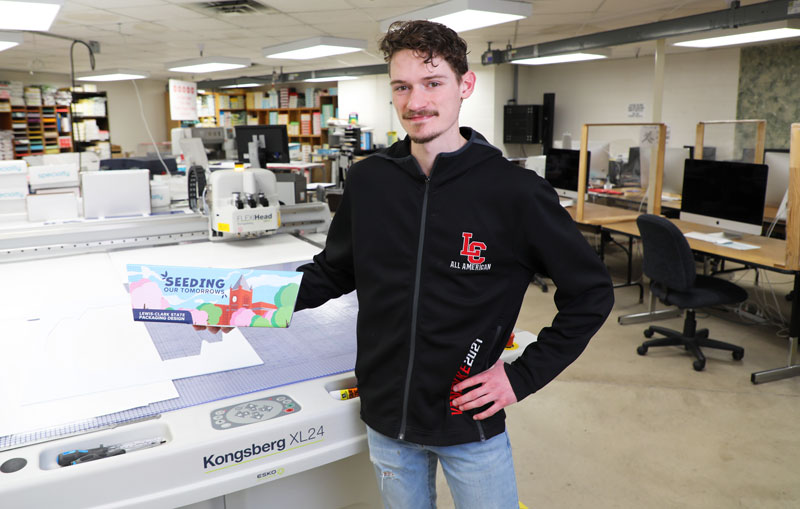
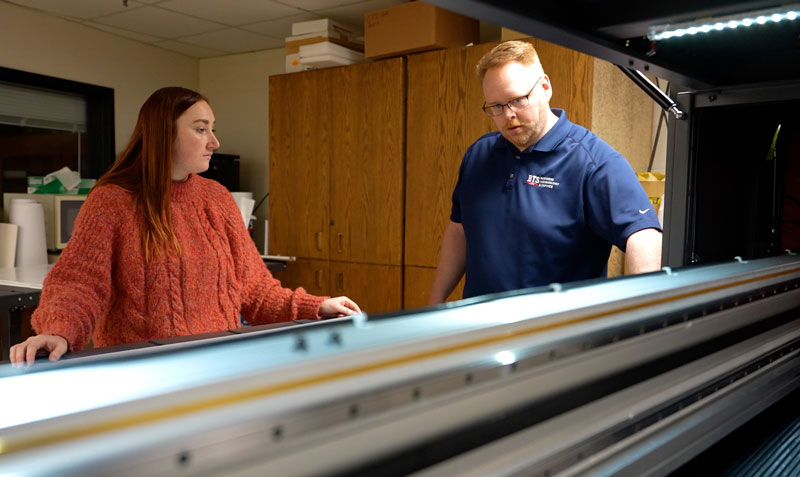
Think of all the packaging you come into contact with every day. Everything from the bottle that holds your shampoo to the tube that holds your toothpaste to the carton that holds your milk had to be designed by someone. And thanks to Assistant Professor Andy Tuschhoff, there’s a chance that the box that holds your cereal was designed by a graduate of Lewis-Clark State College’s (LCSC) Packaging Design program.
Tuschhoff began teaching at LCSC 18 years ago after the commercial printer he worked for in Boise closed.
“My supervisor at the print shop planted that seed when he told me I was really good at my job and should teach my craft to others,” said Tuschhoff. “When I moved back up to Lewiston, that seed germinated, and when an instructional aid position in the Graphic Communication program opened up at LCSC, I jumped at it.”
Initially, Tuschhoff taught students how to use graphic design software like Adobe InDesign. But when another faculty member brought in some packaging production equipment, Tuschhoff took to it and began offering packaging production as an elective course.
“Once, I gave a tour of the program to a high school sophomore who wasn’t sure where they wanted to go or what they wanted to do after high school. They looked around and said, ‘This is what I want to do!’ That’s always stuck with me.”
Andy Tuschhoff
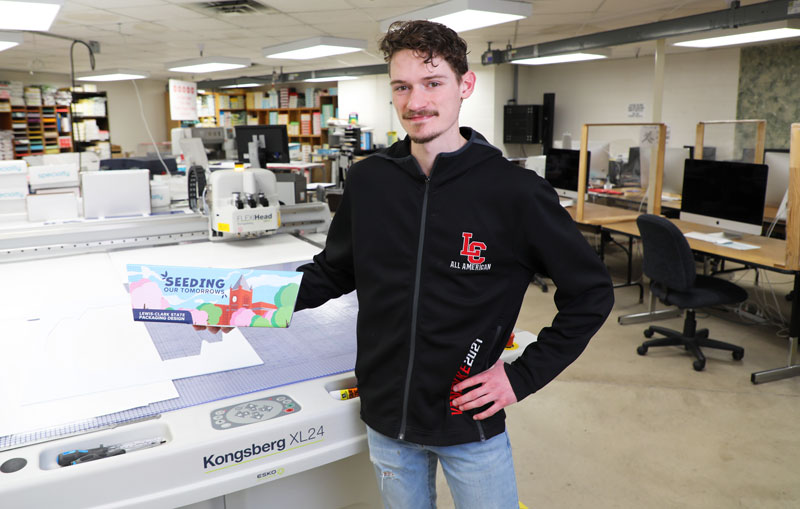
“The Associate of Applied Science (AAS) in Graphic Communication is a good, solid program, but I knew that if we were going to prepare students for the workforce, we had to put more packaging-specific classes behind them,” said Tuschhoff.
Before long, Tuschhoff started taking on more classes and setting up an Intermediate Technical Certificate in Packaging Design. And when Tuschhoff became an assistant professor five years ago, he began developing an AAS in Packaging Design.
“I was able to travel to the WestRock packaging facility in Twin Falls to observe and work with their structural designer for a few days,” said Tuschhoff. “He and their sales manager had invaluable input for course development and expansion, as well as helping us match industry safety protocols in our lab spaces.”
Beyond the principles of design students learn in the AAS in Graphic Communications program, Tuschhoff’s students must learn how those skills translate to three-dimensional structures. The program has a partnership with the International Corrugated Packaging Foundation (ICPF), which has aided in acquiring software and equipment, such as a packaging-specific computer- aided design software called Impact, and a sample table to create true-to-life prototypes. Tuschhoff’s students participate in ICPF’s annual Careers in Corrugated conference and have access to its online career portal to connect with internship and job opportunities. “One of my students landed an internship with a local munition manufacturer’s in-house design team,” said Tuschhoff. “It went so well they were able to offer the student a full-time position.”
In addition to working with industry-standard software and equipment, students can apply what they learn to clients on campus or in the community. Last spring, his students worked with Weiser Classic Candy.
“They’re a pretty well-established company, so the client already knew how he wanted it to be represented, but it was still a cool opportunity for them to create some new container styles,” said Tuschhoff. “Those are currently in production and will be on shelves soon.”
In the future, Tuschhoff would like to see more students coming to LCSC specifically for an AAS in Packaging Design.
“Unfortunately, not enough students interested in graphic design know this career exists. It is so fun, and there’s so much opportunity on both the design and production side of things,” said Tuschhoff. “Once, I gave a tour of the program to a high school sophomore who wasn’t sure where they wanted to go or what they wanted to do after high school. They looked around and said, ‘This is what I want to do!’ That’s always stuck with me.”
North Idaho industrial mechanics program is held in high regard
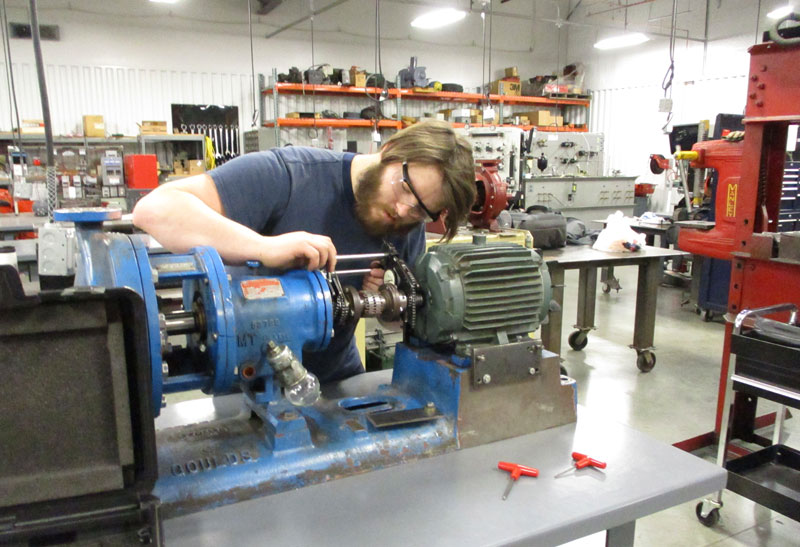
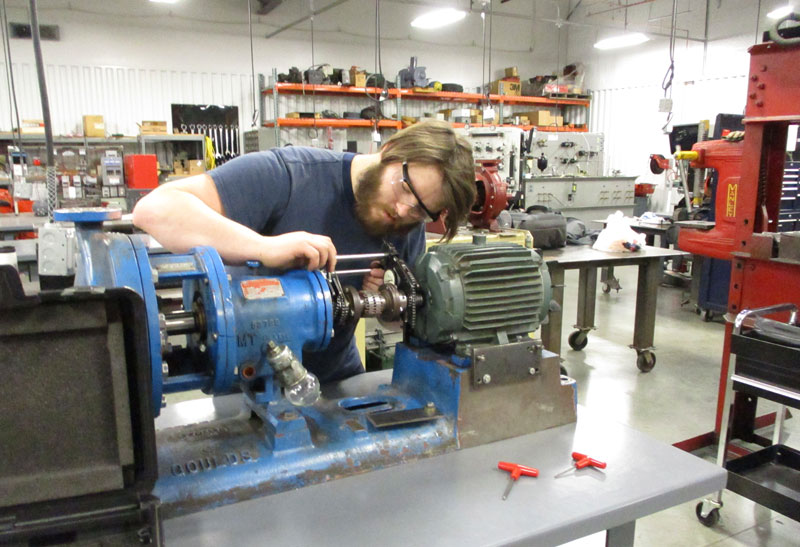
In 2009, high school agriculture teacher Shane Stockham decided to make a big career change and accept a position as the instructor for North Idaho College’s (NIC) Industrial Mechanic/Millwright program. The 11-month program prepares students for employment as industrial plant maintenance mechanics or millwrights. Students learn the basics of maintenance, fabrication, installation, and alignment of equipment used in modern industrial and manufacturing plants.
“They’re the jack of all trades,” said Stockham. “You have to be skilled in a lot of areas, such as welding, hydraulics, electricity, rigging, pipe fitting, and mechanical drive and transmission systems. You’re not doing the same thing all the time, and after 14 years in the classroom, that really appealed to me.”
Though Stockham had a mechanical background and years of experience with farm equipment and welding, he had never been a millwright himself. But he was up for the challenge and spent the better part of 2009 and 2010 boning up on his skills, conducting research, and connecting with industry partners and the previous instructor to help his students succeed. Since the basic requirements of an entry-level millwright are fairly consistent, Stockham made only a few tweaks to the curriculum. One of the most impactful changes he made was having his students visit regional lumber mills and manufacturing facilities two or three times per year.
“Seeing the equipment in action gives them a feel for the work environment and different employers so they can think about whether they’d like to work in that setting,” said Stockham.
“Seeing the equipment in action gives them a feel for the work environment and different employers so they can think about whether they’d like to work in that setting.”
Shane Stockham
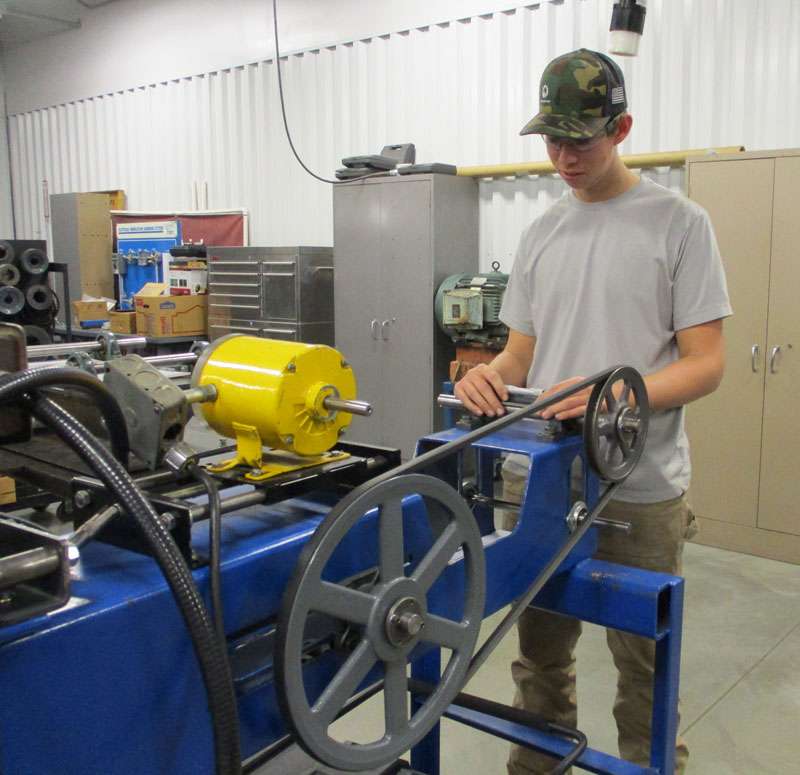
Thirteen years later, Stockham has hit his stride and takes pride in the fact that regional employers hold certificates from his program in high regard. About 90 percent of his students have jobs lined up when they graduate, and industry partners enthusiastically serve on his advisory committee, fund student scholarships, and donate materials. Employers such as the Idaho Forest Group, Stimson Lumber, and Kaiser Aluminum are eager to hire program graduates, and entry-level millwrights can expect to make $27 an hour to start with the potential to make up to $42 an hour once they achieve journeyman status. More experienced graduates have landed employment with the Army Corps of Engineers working on dams along the Columbia River or with Avista Utilities. One student even got hired by Rocky Mountain Construction in Hayden, Idaho, building roller coasters all over the world.
“Anybody who goes through the program is proud of it,” said Stockham. “It’s really hard, but when you look at where you start and where you end up, you have all these skills and can land a great job.”
Though employment opportunities abound, some graduates choose to complete the Mechatronics program and earn their associate degree.
“As everything becomes increasingly automated, mechatronics and mechanics is the wave of the future,” said Stockham. “If students can take the knowledge they learned as a millwright and understand how it drives work and the mechanics behind it, they become much more valuable workers.”
Industrial mechanics provides plenty of variety, opportunity, and competitive wages, but Stockham says his biggest struggle is creating awareness that the program and profession exist. Once potential students have an opportunity to learn about the program, they’re hooked.
“My former students are my best recruiters,” said Stockham. “Word of mouth is huge; many of my students have entered the program because they know someone who was a millwright who encouraged them to check the program out.”
SkillStack® and self-improvement are resident’s formula for success
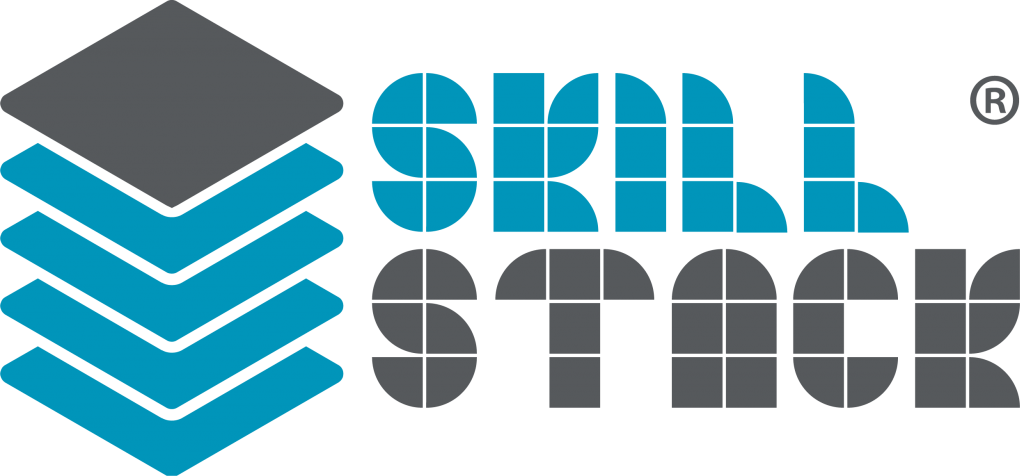
Self-improvement has always been important to Daniel Dives. When Dives worked for Metro by T-Mobile, he always strove to become a better manager and salesperson. But it wasn’t until he read “Unlimited Power” by Tony Robbins and “The 7 Habits of Highly Effective People” by Stephen Covey that he unlocked his potential and realized that business wasn’t about increasing your sales or moving product; it was about developing yourself spiritually, mentally, and physically and teaching others to do the same.
It’s no surprise that Dives was one of 169 unique learners who earned the stacked Administrative Functions microcredential in SkillStack® last year. What is surprising is that he earned it at the Idaho State Correctional Center in Kuna.
Dives is one of 2,777 residents of the Idaho Department of Correction (IDOC) taking advantage of the opportunity to learn industry-recognized credentials and certifications while in residence in 2021. IDCTE partners with IDOC and Workforce Training Centers at each technical college to validate the credentials residents earn.
“Residents can leverage the skills they’re learning to transition to the workforce,” said Taylor Stump, IDCTE’s SkillStack® and performance management coordinator. “Because the credits are transcribed through the technical colleges—and because they’re demonstrating skills aligned with industry standards and credentials—they have a lot of credibility that can help residents upon reentry.”
In addition to learning skills he can use to pursue his career goals upon his release, the classes Dives has taken while in residence have also helped him build his self-confidence. Dives, who has an associate degree in criminal justice, never learned to use Microsoft Office programs, so he’d skip classes if he had to use PowerPoint or wouldn’t speak up in meetings if he had to present.
“When I worked at Metro, we had to run reports two or three times a week. I didn’t know how to create a report, so a lot of things didn’t look right, but they let me wing it because I was good at other things,” said Dives. “As a manager, I’d have rather had my reports look more professional. Had I known then what I know now, I’d have been more confident going to a meeting and saying, ‘This is what I think.’ Before, I would’ve stayed in the background a bit more because I wasn’t confident enough to put myself forward.”
Though Dives has always known he wanted to be an entrepreneur, he’s also taken electrical wiring, electrical systems, and masonry courses through IDOC.
“I wasn’t really planning on going into construction, but it was something positive to do. I like learning, and I like the educational environment,” said Dives. “if you’re going to take classes, you might as well give it your all.”
Daniel Dives
Dives found he liked the hands-on nature of the construction classes and even earned certifications in electrical wiring, electrical systems technology and masonry from the National Center for Construction Education and Research.
“These classes helped me realize I have options and be more open-minded about my future,” said Dives. “There are some guys who’ve been released and come back three times in the five years I’ve been here, and it’s because they don’t have any plans. They don’t have any plans because they don’t think they can do something different. But when you start to realize you are intelligent, you realize you can do these things. You can take these classes. You can have a different future.”
Statewide summary: Over 18,000 students have earned microcredentials
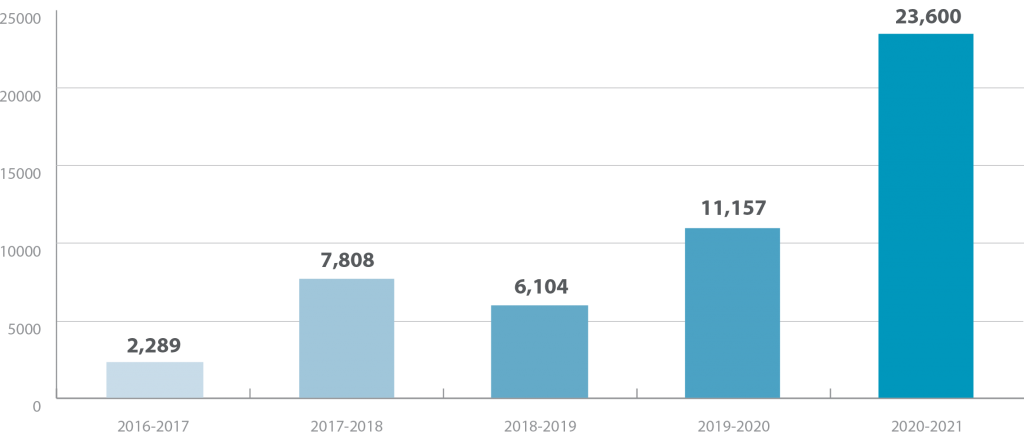
Hard work, determination, translate into career in phlebotomy
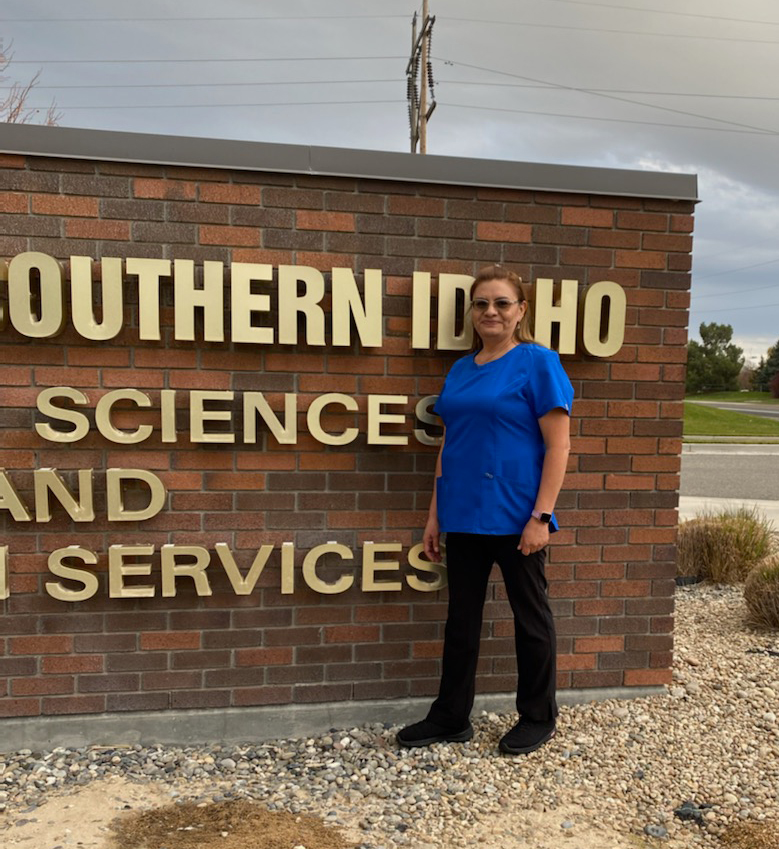
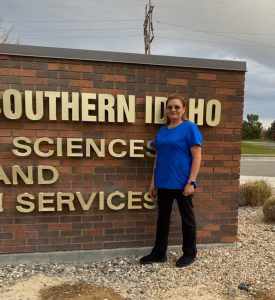
Maria Lopez always knew she wanted to be a nurse. In Mexico City, where she lived before coming to the United States, she even began taking classes. While Lopez didn’t complete her studies, she never abandoned her dream. So when Lopez saw a flyer at the Mexican store advertising the Integrated Certified Nursing Assistant (I-CNA) course at the College of Southern Idaho (CSI), she knew this was an opportunity to make her dream a reality.
At CSI, the I-CNA program is offered through a partnership between its College and Career Readiness (CCR) and Workforce Development Center programs and the Health Science and Human Services department. It is designed to help non-native English speakers learn or improve their English while pursuing their CNA certification. Participants include English-language-learning U.S. citizens, refugees, immigrants, and foreign nationals from various national backgrounds, including countries in Africa, the Middle East, Asia, and Latin America.
“Because the program integrates English language and civics instruction into the standardized CNA curriculum, it takes a whole semester to complete, as opposed to the eight weeks of the general population version of the CNA class at CSI,” said Philip Valenta, industry training coordinator for CCR. “Otherwise, our students are completing the same clinicals and exams as the students of any other CNA section offered on campus.”
The I-CNA program provides a dedicated English Language Acquisition (ELA) instructor to help students improve their language skills and support them during their CNA instruction. The program also includes support outside the classroom, including securing funding assistance, figuring out transportation and childcare options, and creating study groups. And because the cohorts are small—about 10 students are served each semester—CCR can follow up with program graduates to see how they’re doing, personally and professionally. The program was perfect for Lopez, so she enrolled on Jan. 10, 2021.
Lopez, who has been in the U.S. for 26 years, found the customer service and guest relations skills she acquired working at a casino, first as a housekeeper, then as a desk clerk, translated well to being a CNA. But studying medical terminology in her second language proved to be particularly challenging. Fortunately, her children, ages 17, 35, and 38, have been supportive and encouraging.
“They’ve been incredible. I’m 56, so going back to school was a little hard, especially at my age. But when I begin something, I don’t stop,” said Lopez. “Sometimes, I’d take a picture of something I didn’t understand and send it to my daughter-in-law and have her explain it to me.”
Lopez also studied with her youngest daughter.
“She’ll be graduating early in February, and she wants to be a CNA, too,” said Lopez. “She helps me a lot, and I always practice with her.”
In addition to support from her family, Lopez also appreciates the help she received from her instructors at CSI.
“I had the best teachers. Every patient is different, and they showed me so many ways to get the job done and make sure every patient has a good experience,” said Lopez. “They made everything look so easy, but they also made me feel like I could do it. They were so encouraging.”
Maria Lopez
Through hard work and determination, Lopez finished the I-CNA program in June and passed her exams in August. After getting hired as a CNA at St. Luke’s Magic Valley in September, Lopez decided to take the 80-hour phlebotomy course at CSI, which she completed in December. She continues to improve her skills—in both nursing and English.
“When I was taking the CNA course, I had to read some chapters four or five times in English and one or two times in Spanish. I even downloaded a translation app on my phone to help me,” said Lopez. “But now, in my phlebotomy class, I need minimal translation to understand.”
Lopez loves her new job, but she hasn’t forgotten the importance of customer service and hard work. “It doesn’t matter what language you speak,” said Lopez. “It matters how you do your job, how you handle difficult situations, and how you choose to care for people.”
Relationships, certifications lead to 100% job placement for Diesel Technology program
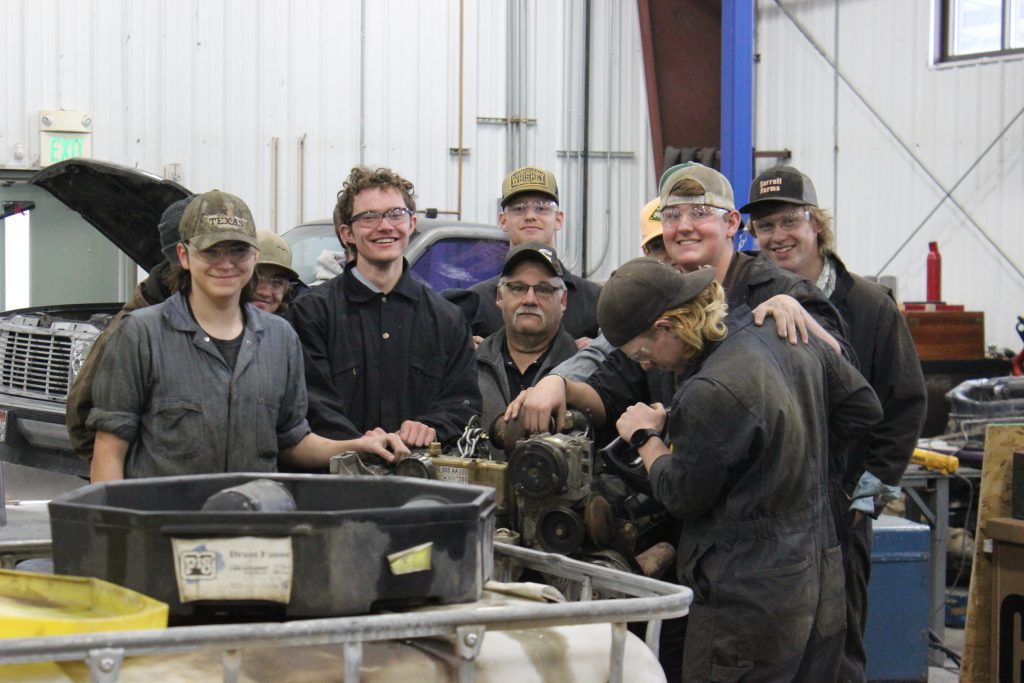
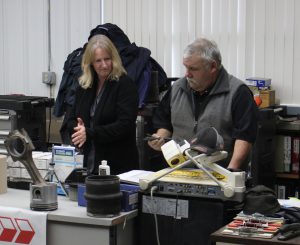
Diesel mechanic John Montana knows firsthand how difficult it is to find skilled workers, especially for in-demand professions. In fact, his inability to find and hire qualified workers is what drove him to become a teacher in the first place.
“I couldn’t hire decent help,” said Montana. “I was training new employees on the job anyway for about 10 or 11 years, so when Canyon-Owyhee School Service Agency’s (COSSA) old diesel technology teacher retired in 1999, I figured I’d give teaching a try.”
Though Montana started teaching part-time, he soon discovered he loved working with the kids and was teaching full-time by his second year. In the two decades since, Montana has cultivated relationships with about a dozen farm implement companies, several of whom employ Montana’s former students. These relationships benefit students and businesses alike—in many ways.
First, industry partners like John Deere, Kenworth, Peterbilt, Agri-Service, Caterpillar, and Mountain View Equipment are always willing to drop off equipment and provide opportunities for students to develop their skills via job shadowing and internships. They know they’ll be able to hire skilled workers from the talent pool Montana produces, so they’re willing to help his students develop career readiness skills by conducting mock job interviews or reviewing student resumes.
Second, industry partners provide additional feedback about new workers’ skills and what needs to change or be updated in the program to prepare students for their careers. This also helps ensure Montana himself stays current.
“That’s one positive thing about these kids staying local; they’re an excellent reference for me,” said Montana. “I don’t get to work out in the field like I used to, so I bounce stuff off my former students all the time. I know I can call any of them up and ask, ‘What have you run across?’ or ‘We’ve got this truck in here that’s doing this and this; have you seen anything like that?’”
Most importantly, these relationships have resulted in 100% job placement over the past 14 years.
“Because the program teaches to NATEF standards, students can earn industry-recognized certifications in electrical engines, transmissions, engine repair, brakes, and preventative maintenance,” said Montana. “Students can also earn their OSHA 10 card and SP2 Safety and Pollution Prevention training certificates while still in high school. That means students may not need a lot of on-the-job training after they graduate.”
This is a huge advantage to not only students but their employers as well.
“If there are 50 applicants for a job and you have these certificates—especially the safety certificates—you’ll move to the top of the list because it cuts down on the number of hours an employer has to train you, and you can get right to work,” said Montana.
Patricia Frahm
COSSA’s principal, Patricia Frahm, says the importance of this foundation can’t be overstated. “If a student walks out of a CTE program with these certifications, they can walk into a job immediately, and if they decide to go on to college, it gives them a skill they can use to pay their way through school,” said Frahm. “They also learn work ethic and accountability in the process—things that can help them for the rest of their lives.”
High school fire program helps fill workforce need in the Portneuf Valley
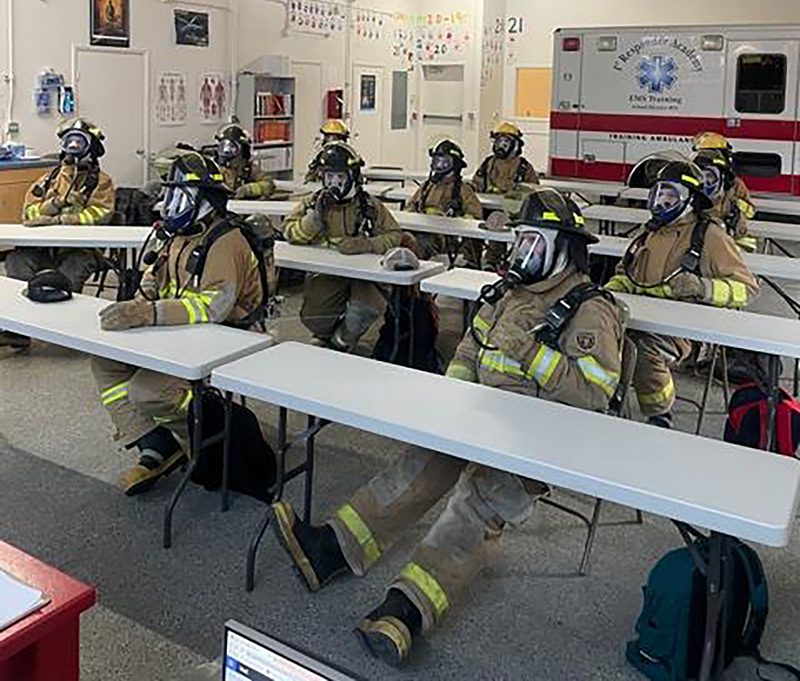
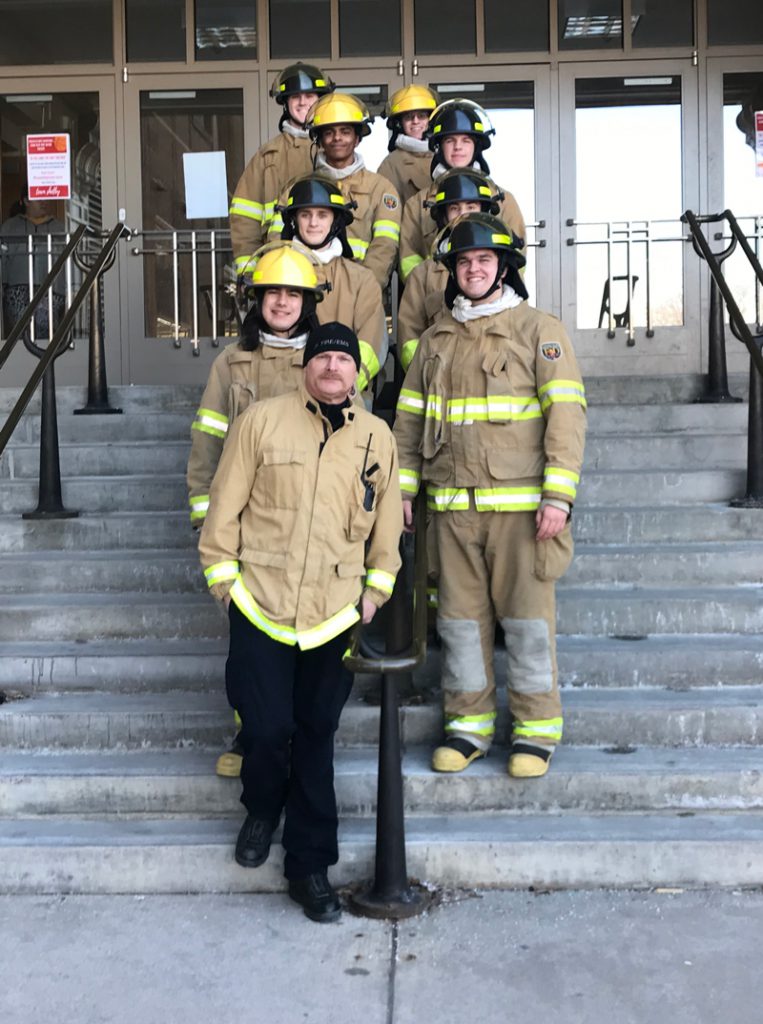
When veteran firefighter Mark Brood agreed to do a presentation on volunteer firefighting at Pocatello High School in 2015, he had no idea where it would lead.
“Right after my presentation, I got hauled down to the principal’s office,” said Brood. “Lisa (Delonas) told me they had a first responder academy, but they didn’t have an EMT or a fire component. She asked if I would be interested in helping get it up and running. I guess it was a case of being in the right place at the right time.”
In his 29 years in the fire service, Brood had trained a lot of new firefighters, so he was up for the challenge. As an active fire chief with the North Bannock Fire Department, he could also rely on his industry connections to establish the program. Fortunately, Brood received much support from Superintendent Dr. Douglas Howell, the school board, the school district, and the fire community. Throughout Eastern Idaho, donations poured in, including turnouts (the protective gear worn by firefighters) from the city of Chubbuck, various equipment from the city of Pocatello, and fire hoses from the Idaho Falls Fire Department.
One of the reasons the community rallied around the program is the growing need for first responders and the fact that so many small communities in Idaho rely on the service of volunteer firefighters.
“In these communities, shopkeepers, farmers, ranchers, and neighbors just drop whatever they’re doing when the bell rings and hop on the fire truck as it goes by,” said Rhonda Naftz, career technical education administrator for School District No. 25. “It’s like training them to fulfill their civic duty. This CTE program can bring this service to smaller communities.”
The Pocatello/Chubbuck School District renovated a building to house the career technical school program and purchased a retired fire engine using Perkins funds. Brood built all the other props necessary for the program, so it was ready to accept its first students when the 2016-2017 school year began.
“When you walk into the classroom, I wanted it to feel like you were walking into a fire department,” said Brood. “I teach to International Fire Service Accreditation Congress (IFSAC) standards. We start each class with the textbook and didactics, then get into the skill work. We try to do everything just like in a fire department, including breaking the class into three platoons, each with its own captain.”
Every day, Brood’s students go through all the equipment to make sure it’s ready and even participate in timed drills, like putting on all their gear in under three minutes. Just like in a real fire department, they have competitions to see which platoon finishes first. Students also can assist on calls, do a ride-along and practice practical skills towards the end of the program.
“The need for first responders is only going to increase as Idaho’s population grows, and this program helps to fill some of that need,” said Brood. “Now that we’re six years into the program, we’re starting to get success stories, which is really cool. I love it when you see a student achieve their goal, or even better, achieve something they didn’t think they could do.”
Mark Brood
Everything about the program is designed to ensure students are prepared to be first responders upon graduation. For example, Brood follows the Candidate Physical Ability Test curriculum, the recognized standard for measuring an individual’s ability to handle the physical demands of being a firefighter. Also, all students earn the National Heart Association CPR for Healthcare Providers certification. Finally, most students take the firefighting course as juniors and the EMT course as seniors because most fire departments require EMT certification.
Upon completion, students have received training to earn their IFSAC and National Wildfire Coordinating Group certifications in Hazardous Materials, Extrication, and Wildland Fire. Students still have to take the industry test, which involves the use of a specialized burn trailer. Students need to be 18 and graduated from high school to complete this component; this activity is usually completed the summer following graduation.
As proof of Brood’s students’ achievements, the SkillsUSA chapter he advises swept the podium during the 2019* state competition. After graduation, many of the students begin their careers with municipal or volunteer fire departments, the Bureau of Land Management, or the U.S. Forest Service, and one student went on to graduate from the Idaho Police Officer Standards Training.
LCSC grad takes over Collision Repair Technology program
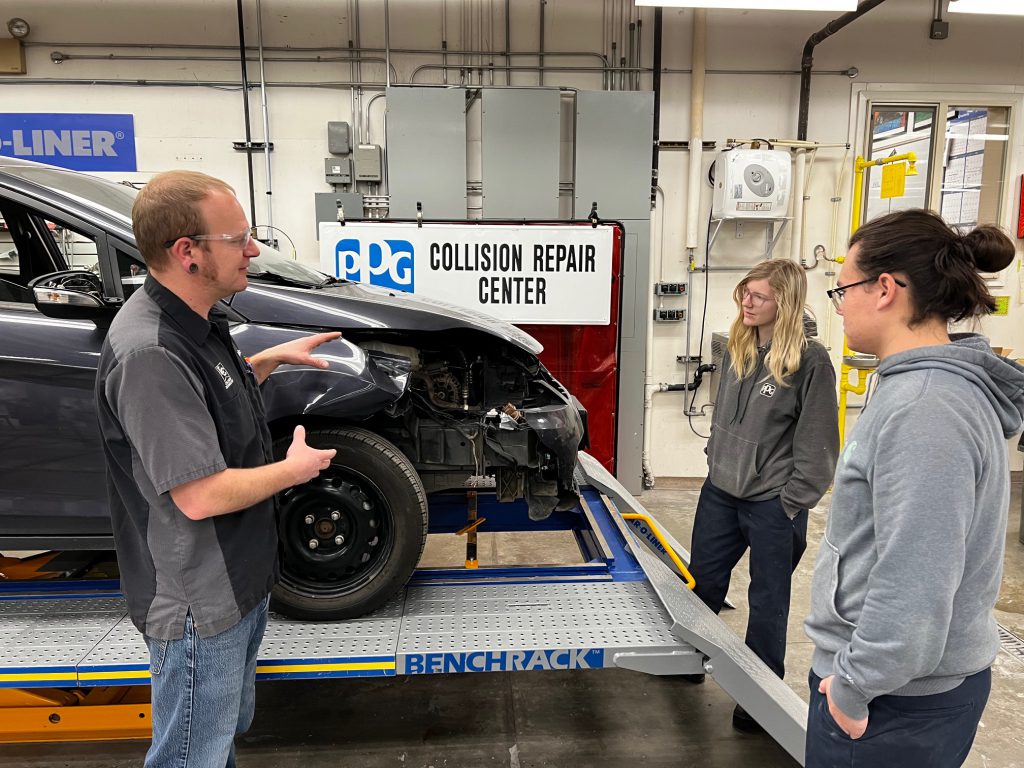
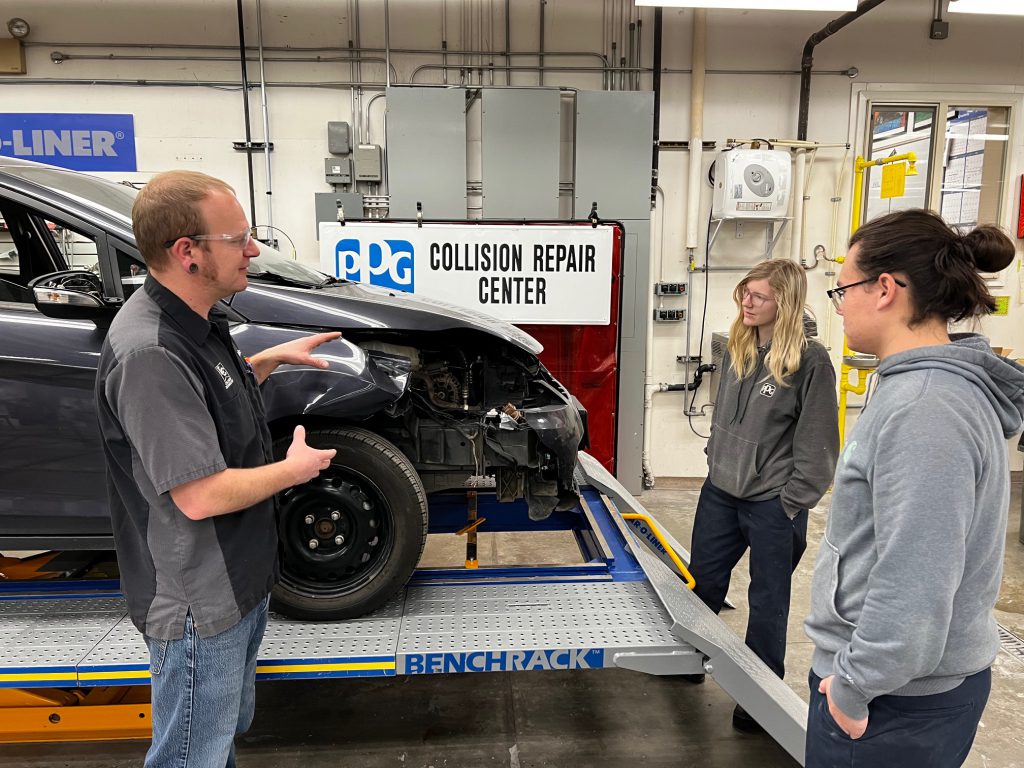
Growing up in the unincorporated town of Laclede, Idaho, Luke Thomas didn’t know what he wanted to do after high school—but he did know he loved working on cars.
“We had a neighbor who worked on cars, and he helped me restore my first vehicle,” said Thomas.
From then on, Thomas was hooked. A family friend who taught at Lewis-Clark State College (LCSC) recommended its two-year Collision Repair Technology program. The program’s reputation, hands-on application, small class size, and one-on-one time with the instructor all appealed to Thomas, who graduated with an Associate of Applied Science in 2008.
After graduation, Thomas’ career was humming along. He had his own repair shop and worked on custom restorations, but he wanted to explore a different facet of the industry. Around that time, Thomas’ professor, Clarence Griffin, decided to transition to teaching part-time, so Thomas saw an opportunity to teach in the same program from which he graduated.
“I was ready for a change and the opportunity to teach the collision program arose at the right time,” said Thomas. “It sounded like a fun way to change things up and help make a difference in the industry.”
During his first three years teaching, Thomas was grateful to be teaching alongside Griffin. And for the most part, Thomas kept the program the same as when he completed it. During the first year, core instruction is provided, and during the second year, students receive in-depth instruction in more complex systems and hands-on training in mock and customer projects.
“Because it’s a two-year program, students can go beyond just learning metal straightening or crash repairs,” said Thomas. “That means we can focus on more advanced skills, and they can get exposure to more facets of the collision repair industry. They’re qualified for a broad spectrum of industry segments by the end of the program, including some outside the collision field, like aviation refinishing, boat manufacturing refinishing, heavy trucks collision repair, custom cars, and hot rods.”
Luke Thomas
A major component of the program is completing an eight-week internship with a local shop. Many students have jobs lined up after graduation at the shop where they completed their internship, which many keep until they decide to move on. The internship allows employers to tap into a talent pipeline to fill their needed positions, which Thomas says translates into more support for the program. Body shop owners have donated vehicles, parts, and uniforms or provided scholarships for the students, and vendors will come in for demonstrations or product training.
Six years later, Thomas has found what he was looking for as a career technical educator. Teaching gave him the freedom to continue running his repair shop and custom restoration business while having more time to pursue other interests. It’s also given him a more holistic perspective of the industry he loves, deepening his appreciation for it.
Above all, Thomas says teaching has allowed him to share his passion with others. “I like seeing someone make something of themselves,” said Thomas. “It takes a lot of work to complete the two-year program, and it’s very rewarding to see a student who completed the program working in the industry and enjoying it.”
HVAC program provides seamless transition from secondary to postsecondary
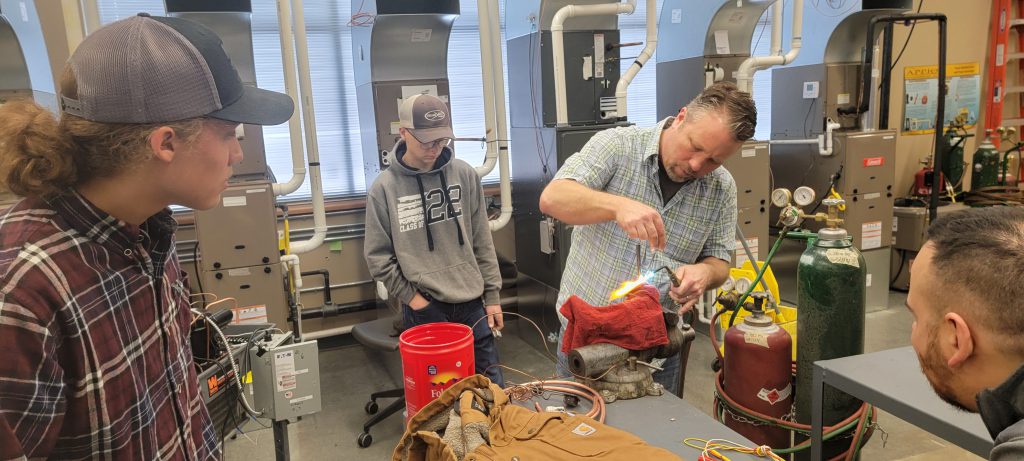
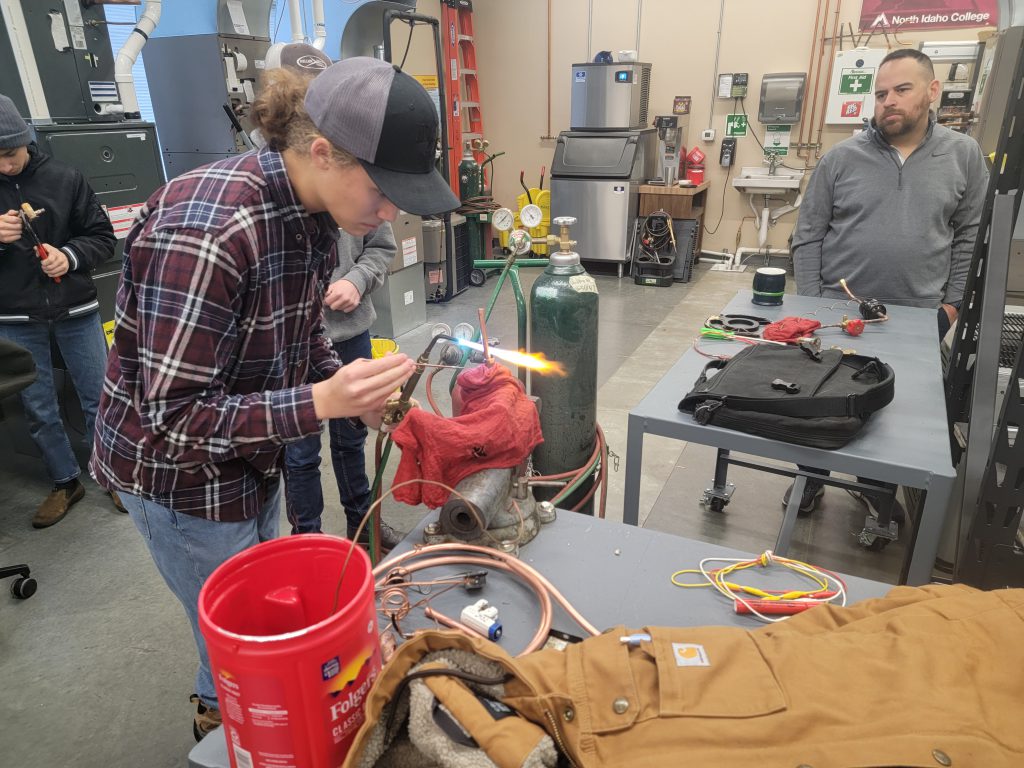
The week before the fall 2017 semester began, Sean Sater received a call from the Trades and Industry Division Chair at North Idaho College (NIC), Doug Anderson. Anderson wondered if Sater would be willing to teach the heating, ventilation, and air conditioning technician (HVAC) class; if Sater said no, the program would be shut down.
Fortunately, Sater, who has 22 years of experience in the field, knew firsthand how much the Coeur d’Alene-Spokane area needed well-trained HVAC technicians. He’d also considered cutting back his hours at HollisterStier, where he worked as a consultant, so he agreed.
“I thought it was a great way to pay it forward and help the next generation change their stars,” said Sater.
Though his first year was a baptism by fire of sorts, Sater enjoyed teaching. So when Anderson, who also served on the board of Kootenai Technical Education Campus (KTEC), asked if Sater would be interested in teaching HVAC at the secondary level the following year, he again agreed.
“I was head over heels to get a hold of them early and get them trained up right,” said Sater. “When we first sat down, we didn’t want the HVAC program to be a huge expense, so we decided it would be best to let the KTEC students use the NIC lab. It’s within walking distance, and we didn’t have to bring in more equipment, which helped us strengthen the partnership between the secondary and postsecondary programs. It was a win-win-win for the students, the schools, and the taxpayers.”
Next, Sater had to strike a balance between offering enough dual credit to make the HVAC pathway appealing to secondary students but not reducing the course load so much that students wouldn’t be considered full-time students and not qualify for financial aid once they transferred to NIC. Sater settled on offering the three-credit HVAC 165 course for his KTEC students, making it easy for them to transition to the second semester’s coursework at NIC.
Sater’s unique position at KTEC and NIC means he can ensure his students have a seamless path from secondary to postsecondary to career. And because there is such a demand for HVAC technicians, employers are eager to speak to his classes and offer opportunities for his students to job shadow or do ride-alongs with their employees.
“It gives them a chance to see if an employer’s culture fits what they’re looking for,” said Sater. “They can talk with industry professionals and see how they operate, keep their vans, and figure out if it would be a good fit—and they get paid to do so.”
Sean Sater
These interactions with employers mean most postsecondary students in their second and final semester know where they want to work and have a job lined up after graduation. The jobs Saters’ students walk into don’t exactly pay minimum wage, either.
“They’re paying $9,000 for books and tuition and can be making $52,000 a year to start, without the baggage of student debt,” said Sater. “That’s a pretty solid return on investment.”
At the end of the day, Sater loves knowing he’s setting future professionals up for success while helping to meet industry needs.
“I love the feeling of getting through to someone,” said Sater. “They might ride the struggle bus for a while, but when things come together, they learn it and burn it into their memory. It’s priceless to see the light come on.”
CTE helps horticulture student’s passion and career bloom
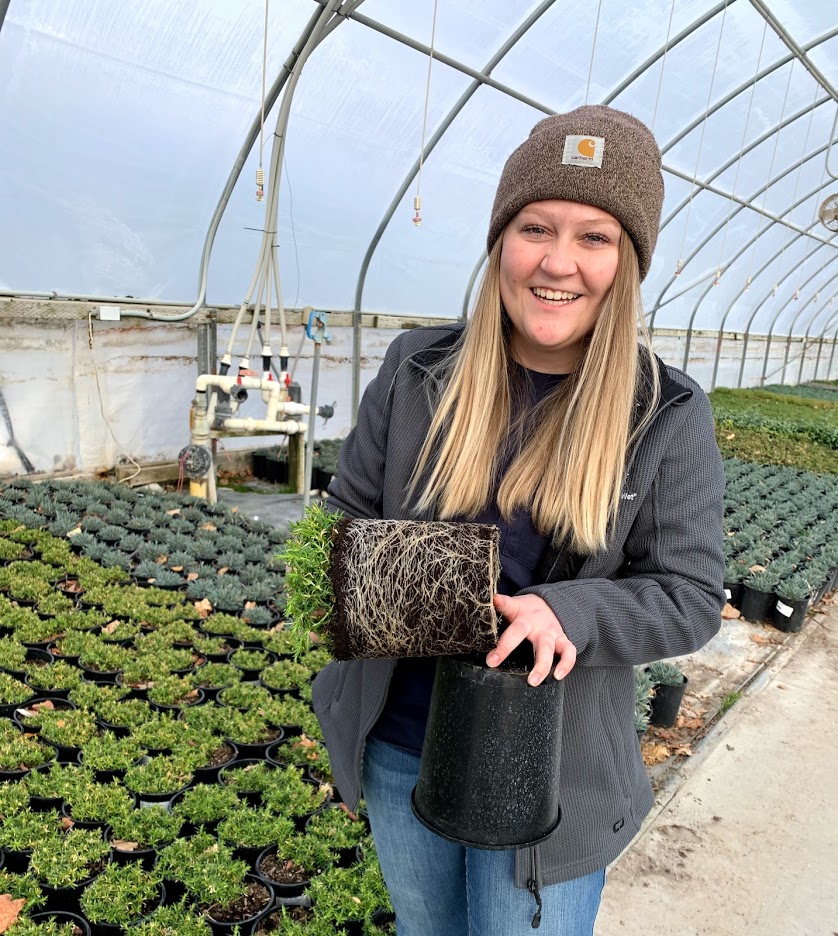
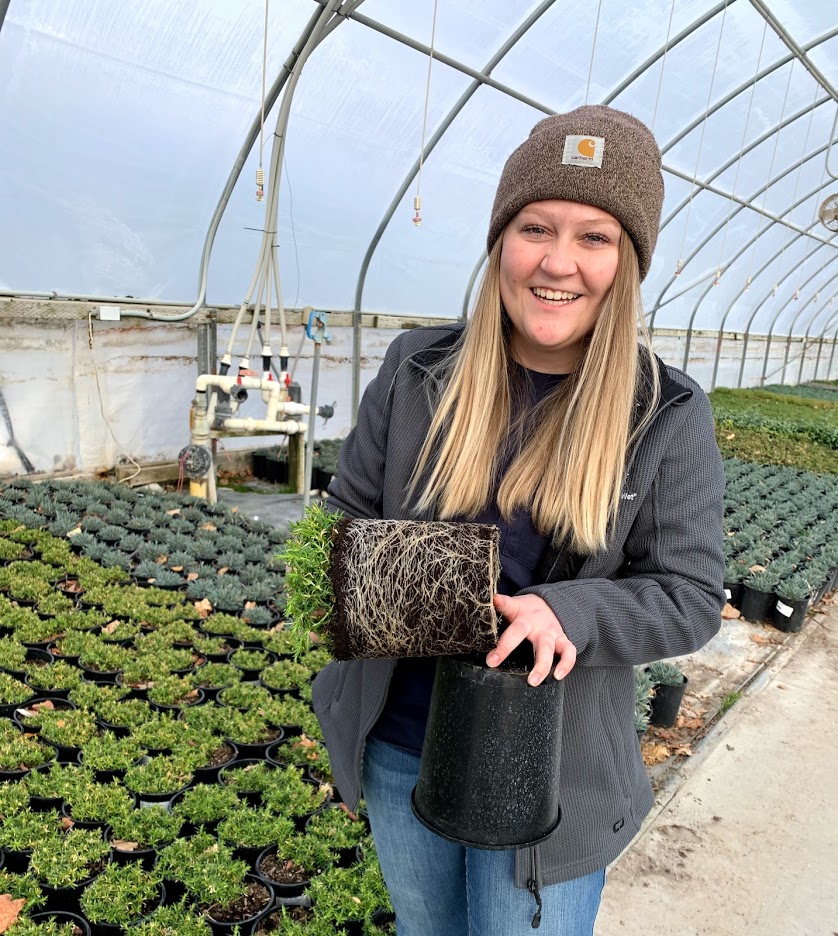
“I love my job. I love getting to work with plants and watch them change throughout the year.”
Ellie Garrard
Ellie Garrard didn’t set out to be a horticulturist. When she graduated from Burley High School in 2017, she chose to go to the College of Southern Idaho (CSI) because it was close to home. She was introduced to the idea of horticulture from one of the leaders of her youth group at church who had a degree in horticulture, and Garrard was fascinated with the massive gardens she kept.
“I liked that she could make her own schedule, and she really inspired me to work with plants,” said Garrard.
But it was not the image of perfect gardens that made Garrard decide to pursue a degree in horticulture herself—it was the idea of climbing trees with a chainsaw.
“I’m kind of a small person; I’m just five feet tall,” said Garrard. “But the thought of someone like me being able to climb a tree with a chainsaw like any big, burly man kind of excited me.”
Garrard soon fell in love with the different ways to climb trees. Her professor, Chance Munns, taught her how to tie different knots and use lanyards to climb trees. For one class, Garrard got to climb one of the biggest cottonwood trees on campus; she was one of the only students to reach the top.
“I was so excited! It made me want to buy climbing equipment and a chainsaw,” she said.
To make sure horticulture was a good fit, Garrard interned for a tree pruning service one summer. She learned how to completely take down trees, install sprinkler systems and lay sod.
“I loved it, but it was really hard on my body,” she said. “In the process, I discovered I was really good at pruning fruit trees, though.”
While Garrard pruned fruit trees for friends and neighbors while she was going to CSI, she had no idea it would eventually play a large role in her career. When Garrard graduated from CSI with an Associate of Applied Science degree in horticulture in the spring of 2019, she moved home for a few months to plot out her next move. Her mother ran into an acquaintance from church who owned Teton Trees. They had an opening for a pesticide applicator that had gone unfilled for months.
“As it turned out, pesticide application was the only class I wasn’t able to take at CSI,” said Garrard. “But the position had been open for several months, and they said they were willing to train me, so I took it.”
At first, Garrard was hesitant because the pest control side of horticulture was so new to her.
“I also didn’t know how much I’d remember from school. I didn’t know the names of all the weeds and leaves or how to determine what kind of bug was causing damage, but I kept at it,” Garrard said.
Her hard work paid off, and Garrard was soon promoted to assistant grower of plant health.
“When I realized I did have the training and knowledge that were needed in a plant health position, those skills—like pruning—really came back,” she said.
In fact, Garrard wrote Teton Trees’ employee pruning guide to ensure all pruning crews were following the same standards companywide.
“At our smaller location, we only have one or two pruning crews, but in Paul, there are three or four pruning crews, and many of them only speak Spanish,” Garrard said. “I wrote the guide and worked with some translators to ensure all our employees were following the same standards.”
Like the plants she tends, Garrard is thriving in her new role.
“In horticulture, there’s a lot of on-the-job training, and we learn a lot from consultants,” said Brett Bingham, Teton Trees’ general production manager and Garrard’s supervisor. “Ellie has a great attitude, and she caught right on. She helps with soil fertility, plant health and pesticide application. She knows what to look for and communicates with other professionals to get her job done.”
Garrard may not have set out to grow picturesque gardens, but as it turns out, she’s still surrounded by beauty.
“I love my job. I love getting to work with plants and watch them change throughout the year. In the shrub yard in the fall, the color stays pretty for a long time,” said Garrard. “I’m always surrounded by acres and acres of pretty plants.”
ISU robotics program prepares grad for career and promotions
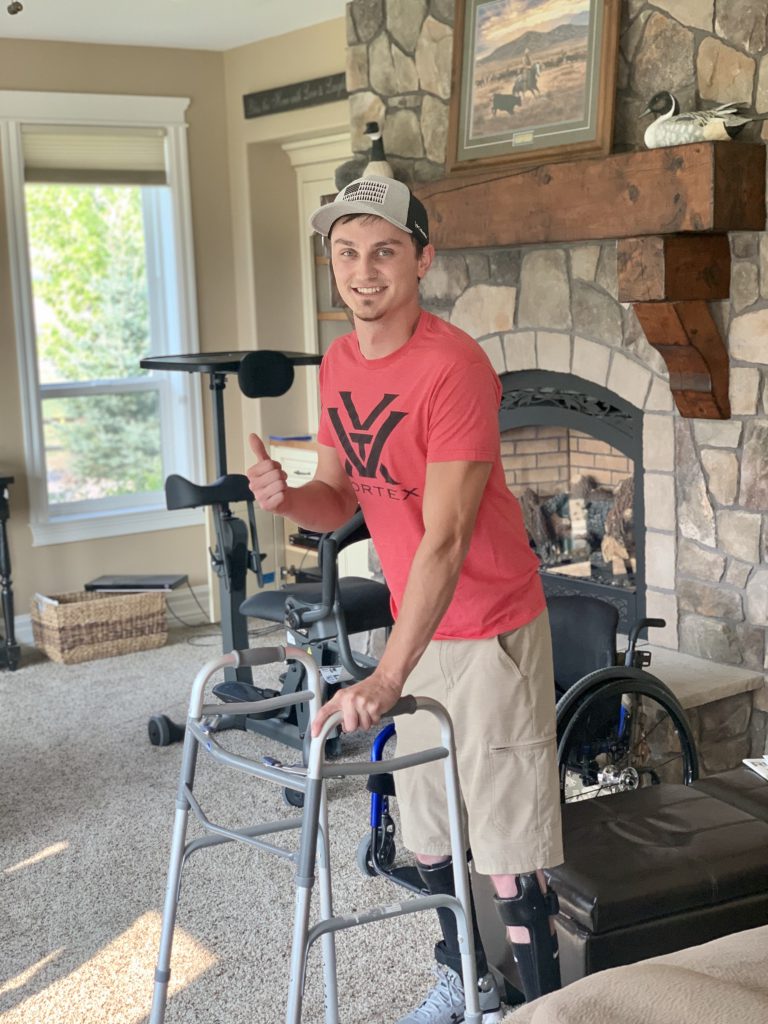
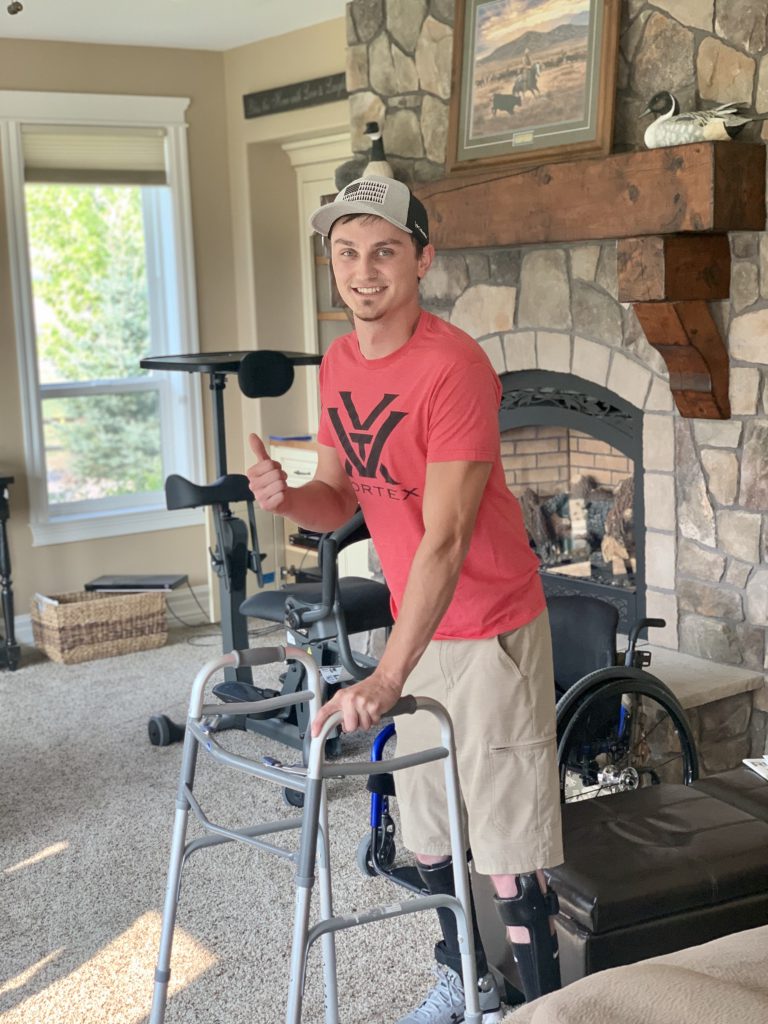
“The equipment I used at ISU is exactly what I use at Inovar. I felt they taught me what I really needed to know, and I didn’t have to learn on the job.”
Will Treasure
Treasure’s father, Dave, used to teach welding at ISU’s College of Technology, so he grew up on the ISU campus.
“My dad was always showing me programs at the College of Technology, and I always thought it was a cool place,” said Treasure. “I knew I needed a career where I didn’t have to lift anything, so my dad encouraged me to check out the robotics program.”
Instructors Shane Slack and Geran Call gave him a tour, and Treasure was hooked.“At first, I thought it was really nerdy, but the lab had interesting stuff like a real R2-D2, drones, and a 3D printer. The more I thought about it, the more I realized that robotics is part of everything. It’s in your phone; it’s in your car; it’s in anything electronic. I felt like the program could teach me to fix just about anything, and there was no shortage of job opportunities,” said Treasure.
The six-semester program did not disappoint.
“The instructors really know their stuff. One day, I was trying to figure out some coding. Shane looked at it and said, ‘That’s pretty good,’ but then he showed me some tips and tricks and I was able to cut the code in half.”
In addition to small class sizes, hands-on projects, accessible instructors and progressively more complicated coursework and projects, Treasure also appreciated the collaboration between other programs at the College of Technology.
“All of the trades and techs are really well put together,” said Treasure. “You see all the programs working together and willing to help one another.”
Treasure completed his degree in robotics and communications engineering systems technology in the fall of 2018—and he had a job lined up after graduation.
“Around the fifth or sixth semester, they encouraged us to start looking for jobs. Shane helped us with our resumes, and they were constantly bringing in potential employers for on-site interviews,” said Treasure. “It was really easy to find a job because these employers had such good experiences with previous graduates.”
Treasure accepted a position at Inovar in Logan, Utah, specializing in electronic manufacturing services for military and medical equipment. At first, Treasure worked as a service technician fixing boards at the component level. Thanks to the program at ISU, Treasure feels he was well prepared for the job.
“They expected so much out of us, and they always wanted us to do things the right way,” said Treasure. “The equipment I used at ISU is exactly what I use at Inovar. I felt they taught me what I really needed to know, and I didn’t have to go through so many hoops to learn on the job.”
The combination of being well-prepared for his career and passionate about his work led to Treasure being offered a promotion in November 2020.
“Drawing schematics at school and knowing how things functioned at work helped me get this promotion,” said Treasure. “I started at Inovar with another classmate. A lot of people asked us where we went to school because they wanted more employees like us. I have nothing but good things to say about my experience at ISU.”